Filling Monoblock for production up to 2.000 bph from 5 Lt to 5 Gallon
The Trevi Twin features have been transferred also on a linear block, for smaller production up to 2.000 bph.
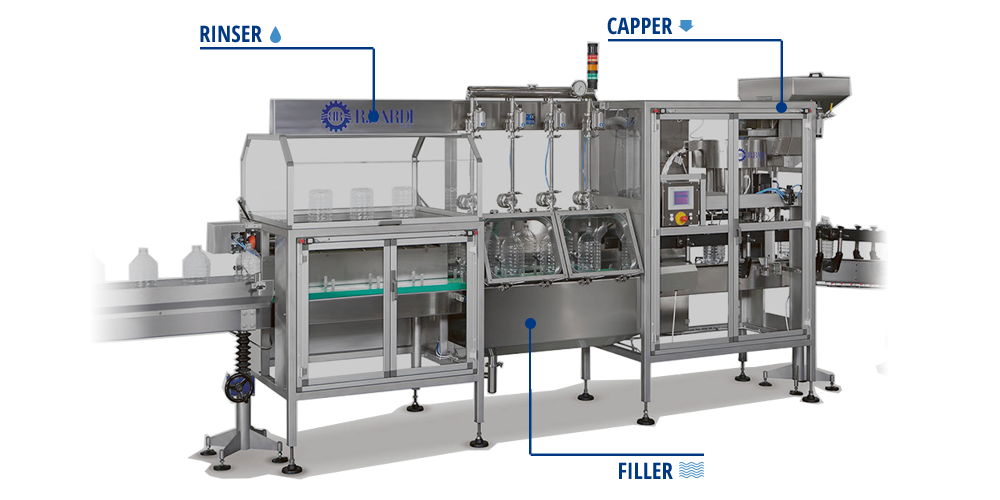
Bardi can offer 2 alternative solutions:
- In case of manual feeding of the bottles, we can supply a rinser which can ensure a strong cleaning action on the bottles, through:
- A first treatment of sterilization, through ozonated water
- A second rinsing through filling water or filtered air
- In case of direct blowing of the bottle in line, we can supply the monoblock without any rinser but with a closed and pressurized tunnel conveyor.
The Bardi filler, according to the Ultra-clean design, has the following features:
- The filling process avoid the contact between the valve and the neck of the bottle (risk of contamination transfer).
- The filling valve and all the piping, valves etc. in contact with the product have a sanitary design and made of aisi 316 S.S.
- The filling process is electronically controlled so has to guarantee the accuracy of filling and to limit the water consumption.
- The cabinet doesn’t present dead ends, according to the strictest hygiene design requirements.
- The filling cabinet is equipped with overpressure air flow. A minimum class 1000 air filtration should be guaranteed, so as to protect the filling environment from the external ambient contamination. On request certified class 100 filtres are available (see the pictures below).
- If present, rinser and filler are in block in order to avoid the potential contamination of the clean bottles travelling from the rinser outlet to the filling area.
- All mechanical and pneumatic gears have been installed outside the cabinet.
- All parts and surfaces in contact with the product are prearranged for 3 or 5 steps CIP (cleaning in place) sterilization treatment; the CIP system can be automatic or semi-automatic and can works with hot or cold solution (see the picture on the right)
The electronic screw capper stands out because of its operating simplicity and precision.
- The system doesn’t require stars, mechanical clutches, or complex lifting mechanisms.
- The closing torque can be set from touch screen; the vectorial frequency converter allows to manage it with high precision.
- The handling parts to move the bottle in the machine are reduced to the minimum, so as the change-over downtimes.
This machine is provided with a new system for bottle size change which:
- Allows to use filling valve and all the piping, valves etc. in contact with the product with sanitary design and made by AISI 316 S.S. (without flexible piping)
- Is immediate, can be handled easily through the PLC and it doesn’t involve any time wasting
- Doesn’t require physical effort or technical knowledge